Introduction: Steam rubber hoses are essential components in various industries where steam is used for numerous applications. Over the years, innovative advancements in materials and design have revolutionized the performance of these hoses, increasing their durability, flexibility, and overall efficiency. In this blog post, we will explore the latest innovations in steam rubber hoses, highlighting how these advancements contribute to improved performance in industrial settings.
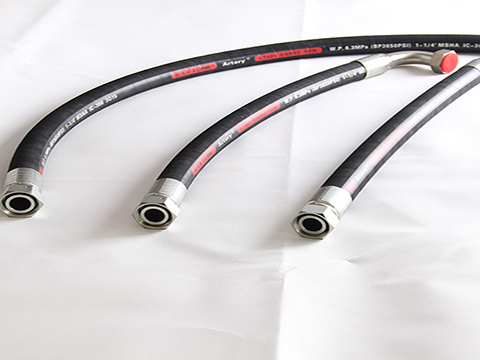
- High-Temperature Resistant Materials: One significant innovation in steam rubber hoses is the development of high-temperature resistant materials. Traditional rubber hoses were limited in their ability to withstand extreme heat, often resulting in premature degradation and failure. However, with the introduction of advanced materials such as EPDM (ethylene propylene diene monomer) and synthetic blends, steam rubber hoses can now withstand higher temperatures without compromising their structural integrity. These materials provide excellent resistance to heat, ozone, and aging, ensuring longer hose life and improved performance in high-temperature applications.
- Reinforcement Technologies: To enhance strength and durability, steam rubber hoses are often reinforced with various technologies. One notable innovation is the use of high-tensile strength synthetic fibers or steel wire braids. These reinforcement methods significantly increase the hose’s burst pressure and resistance to internal and external pressures, ensuring safe and reliable steam transport even under demanding conditions. Reinforced hoses also exhibit improved flexibility, allowing for easier installation and maneuverability in industrial settings.
- Anti-Static Properties: In certain industrial applications, static electricity can pose a significant safety risk. To mitigate this, innovative steam rubber hoses incorporate anti-static properties. These hoses are designed with conductive layers or compounds that dissipate electrical charges, preventing the build-up of static electricity. By eliminating the risk of electrostatic discharge, these hoses ensure a safer working environment and reduce the potential for accidents and injuries.
- Enhanced Flexibility: Another area of innovation in steam rubber hoses is the improvement in flexibility. Traditionally, rubber hoses were relatively stiff and challenging to maneuver, hindering installation and operation. However, modern advancements have resulted in hoses with increased flexibility without compromising their structural integrity. Enhanced flexibility allows for easier handling, routing, and connection to equipment, saving time and effort during installation and maintenance procedures.
- Extended Hose Lengths: In industrial settings, the ability to transport steam over long distances is crucial. Innovations in steam rubber hose design have led to the availability of extended hose lengths, enabling efficient steam distribution across large areas. Longer hoses reduce the need for additional connections and joints, minimizing potential leakage points and improving overall system reliability. This advancement contributes to optimized steam flow, reduced energy loss, and enhanced operational efficiency.
Conclusion: Innovations in materials and design have greatly improved the performance of steam rubber hoses in industrial applications. High-temperature resistant materials, reinforcement technologies, anti-static properties, enhanced flexibility, and extended hose lengths are just a few examples of the advancements that contribute to the durability, reliability, and efficiency of these hoses. By embracing these innovations, industries can optimize their steam systems, improve safety, reduce downtime, and enhance overall productivity.